MDPI Sensors, the renowned journal on the science and technology of sensors, accepted three different SocketSense manuscripts on topics related to the technological advancements of our developing innovative advanced sensor-based socket system. More specifically, the joint research publications are part of the special issue “Increasing Prosthetic Comfort through Sensor Technology” that belongs to the section “Biomedical Sensors”. So, let’s take a closer look at the SocketSense publishing accomplishments.
TWI Hellas, in collaboration with KTH Royal Institute of Technology, produced a research paper on the SocketSense Sensor-Based Decision Support System (DSS) for Transfemoral Socket Rectification[1]. This manuscript aims to showcase the design of the DSS, the processes it follows, the socket rectification 3D simulation testings, and the value of the results for the final form of the prosthetic socket. Τhe paper’s conclusive finding is that the intensity of discomfort at the stump is affected by the amount of rectification and the pressure distribution within the socket. Thus, the balance between them is crucial to the socket design.’
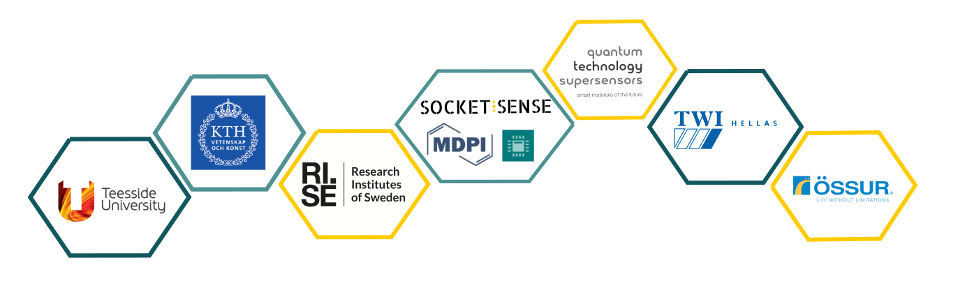
On the topic of sensor design, Össur, KTH Royal Institute of Technology and Teesside University came together to work on a scoping review of the pressure measurements in the prosthetic sockets of transfemoral amputees during ambulation[2]. This publication includes an in-depth analysis of 12 scientific articles to evaluate how sensor systems can progress to become more effective. In more detail, the paper outlines the existent methodology for experimental studies on the intra-socket pressure sensor use for transfemoral amputees. It also suggests the introduction of interdisciplinary collaboration and a more open-access research approach. Moreover, sensor design innovations can be initiated through pressure sensors being developed alongside other types of sensors and with the help of clinical experts in prosthetics.
Last but not least, RISE Institute, in cooperation with Lusstech, focused on manufacturing sensors that can effectively measure pressure, shear and loss of friction/slippage while being low-cost, more environmentally friendly and scalable[3]. These prototype sensors have been made from magnetite-based QTSS™ (Quantum Technology Supersensor™) quantum materials. Their testing during a SocketSense pilot amputee trial showed that they can operate on flat and curved surfaces. They can also detect increasing shear forces and their consequent different directions while identifying loss of friction and slippage events. The research, testing and optimization process will continue as part of the SocketSense project in order to establish a prosthetic lower limb that excels in comfort and fit.
For the full SocketSense publications, click below:
https://www.mdpi.com/journal/sensors/special_issues/prosthetics
[1] Karamousadakis, M.; Porichis, A.; Ottikkutti, S.; Chen, D.; Vartholomeos, P. A Sensor-Based Decision Support System for Transfemoral Socket Rectification. Sensors 2021, 21(11), 3743 https://doi.org/10.3390/s21113743
[2] Ko, S.; Asplund, F.; Zeybek, B. A Scoping Review of Pressure Measurements in Prosthetic Sockets of Transfemoral Amputees during Ambulation: Key Considerations for Sensor Design. Sensors 2021, 21(15), 5016 https://doi.org/10.3390/s21155016
[3] Dejke, V.; Eng, M.; Brinkfeldt, K.; Charnley, J.; Lussey, D.; Lussey, C. Development of Prototype Low-Cost QTSS™ Wearable Flexible More Enviro-Friendly Pressure, Shear, and Friction Sensors for Dynamic Prosthetic Fit Monitoring. Sensors 2021, 21(11), 3764 https://doi.org/10.3390/s21113764